Industrial robotics has redefined the modern manufacturing landscape, bringing about higher levels of efficiency, precision, and productivity. As these automated machines become integral to operations across a myriad of industries, the need for regular maintenance to ensure optimal performance becomes increasingly critical.
This article delves into the importance of routine upkeep, the consequences of neglect, and the implementation of an effective maintenance plan for industrial robots.
Understanding Industrial Robots
Industrial robots are programmable devices designed to carry out a series of tasks within an industrial setting. Brands such as FANUC have pioneered the way in this field, with robots performing roles that range from assembly, painting, welding, to packaging and material handling.
Depending on the nature of the task, industrial robots come in various types, each with unique components and functionalities – all designed to increase productivity, maintain consistent output, and decrease production costs.
Why Regular Maintenance is Essential
Just like any other machine, industrial robots require regular maintenance to stay in optimal working condition. This routine upkeep extends their lifespan and maximizes their efficiency, ensuring that the considerable investment in these machines pays off in the long run.
Regular maintenance also minimizes instances of unplanned downtime, ensuring continuous production schedules and maintaining the overall efficiency of manufacturing operations.
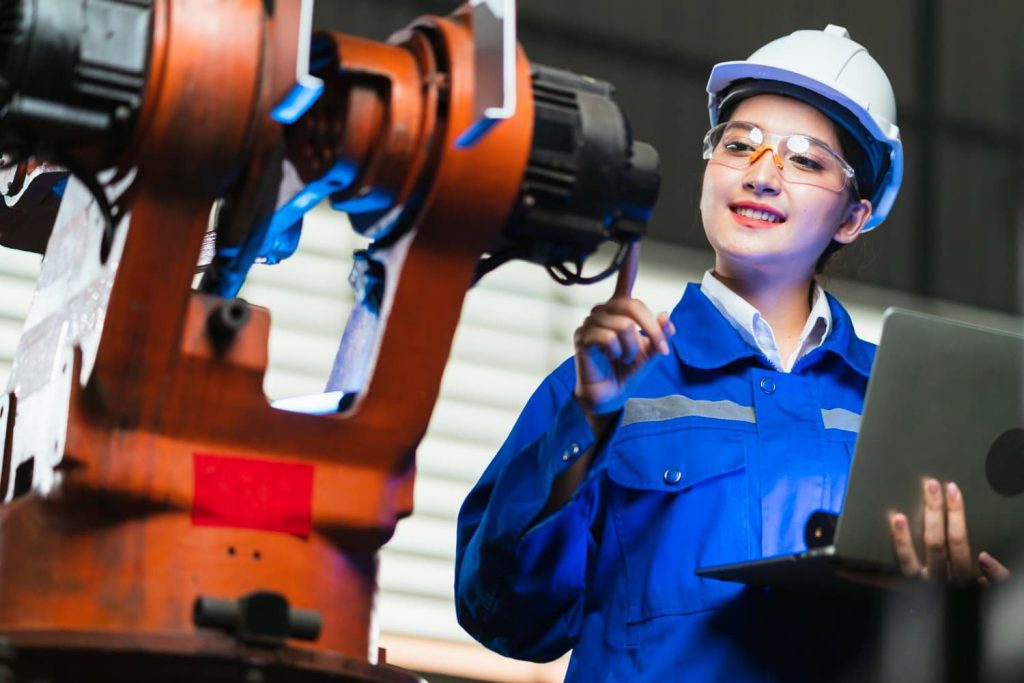
Common Problems That Occur Without Regular Maintenance
Lack of routine maintenance can lead to a host of problems in manufacturing robots. Mechanical parts may wear out, leading to inaccurate movements and compromised output quality. Electrical systems may malfunction, resulting in unexpected shutdowns. Software issues may disrupt operations, causing delays and potential data loss.
These problems not only impact productivity but can also lead to increased downtime and higher costs for repairs and replacements.
Key Areas to Focus on During Maintenance
When conducting regular maintenance, certain areas require particular attention. Mechanical parts, such as joints and gears, should be inspected for wear and tear, and lubricated as needed.
Electrical systems, including wires, connections, and power supplies, should be checked for any signs of damage or deterioration.
The robot’s software should be updated regularly to ensure smooth operation and compatibility with other systems. Additionally, safety features should be tested regularly to ensure the robot operates safely within its environment.
Preventive and Predictive Maintenance
Preventive maintenance involves scheduled checks and upkeep to prevent potential issues before they occur. This can include replacing worn parts, updating software, and thorough cleaning.
On the other hand, predictive maintenance leverages technology, like IoT and AI, to predict potential issues based on data collected from the robot. By monitoring parameters like vibration, temperature, and energy consumption, predictive maintenance can identify early signs of wear and tear, allowing for proactive intervention.
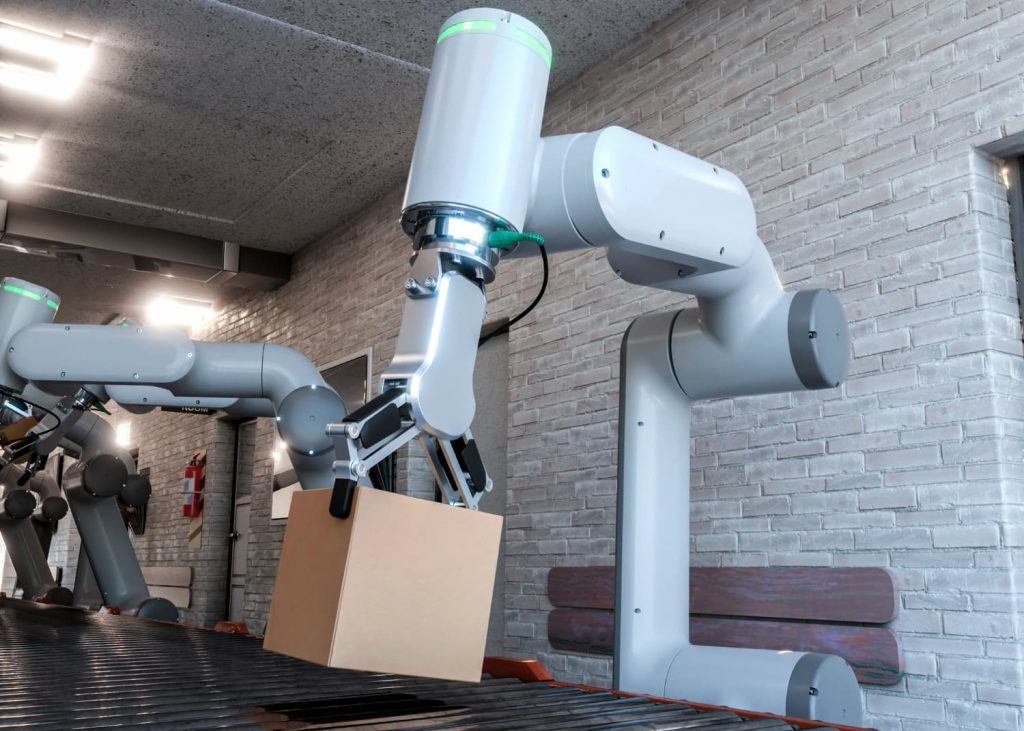
How to Implement an Effective Maintenance Plan
An effective maintenance plan involves scheduling regular inspections, preventive maintenance, and predictive maintenance based on the manufacturer’s recommendations and the robot’s usage patterns.
Proper training should be provided to personnel involved in the maintenance process, and all procedures should be documented for consistency. Using maintenance software can help streamline the process by automatically scheduling tasks, tracking progress, and flagging any issues.
Case Study
Consider the example of a large automotive manufacturing company that experienced frequent production halts due to robot malfunctions. Upon implementing a rigorous maintenance plan, the company reported a significant drop in unscheduled downtimes, an increase in productivity, and substantial cost savings in repair and replacement expenses.
This case study reinforces the importance of regular maintenance in maximizing the efficiency and lifespan of industrial robots.
Wrapping It Up
In conclusion, regular maintenance of industrial robots is critical in ensuring their optimal performance, increasing their lifespan, and reducing overall production costs.
By focusing on preventive and predictive maintenance, manufacturers can mitigate potential issues, reduce downtime, and maximize the return on their investment in robotics. In the rapidly evolving landscape of industrial manufacturing, proactive maintenance isn’t just a good-to-have, it’s an essential strategy that drives operational excellence and competitive advantage.
As the adoption of industrial robotics continues to accelerate, regular maintenance will remain a key aspect of successful and cost-effective manufacturing operations.